Abstract
Kinesthetic garments provide physical feedback on body posture and motion through tailored distributions of reinforced material. Their ability to selectively stiffen a garment’s response to specific motions makes them appealing for rehabilitation, sports, robotics, and many other application fields. However, finding designs that distribute a given amount of reinforcement material to maximally stiffen the response to specified motions is a challenging problem. In this work, we propose an optimization-driven approach for automated design of reinforcement patterns for kinesthetic garments. Our main contribution is to cast this design task as an on-body topology optimization problem. Our method allows designers to explore a continuous range of designs corresponding to various amounts of reinforcement coverage. Our model captures both tight contact and lift-off separation between cloth and body. We demonstrate our method on a variety of reinforcement design problems for different body sites and motions. Optimal designs lead to a two- to threefold improvement in performance in terms of energy density. A set of manufactured designs were consistently rated as providing more resistance than baselines in a comparative user study.
Video
System overview description using the example of the arm flexion as an input motion, and the arm sleeve region as the garment
to be reinforced. From left to right. Input: A designer imports a sequence of body poses and labels the rest pose (zero energy) and final
pose (optimization objective). The garments are defined on the surface of the body. Design Exploration: The on-body topology optimization
produces a sequence of optimal designs as a function of the reinforced area (budget). The background bars represent the area coverage of
reinforcements. Evaluate: Designer picks between two candidates and evaluates them in simulation over the full motion sequence. Fabricate:
the 3D on-body surface design of the reinforce regions is then flatted, cut and heat-transferred into the soft sleeve to produce the kinesthetic garment.
Acknowledgments
This project has received funding from the European Research Council (ERC) under the European Union’s Horizon 2020 research and innovation programme grant agreement No. StG-2016-717054.
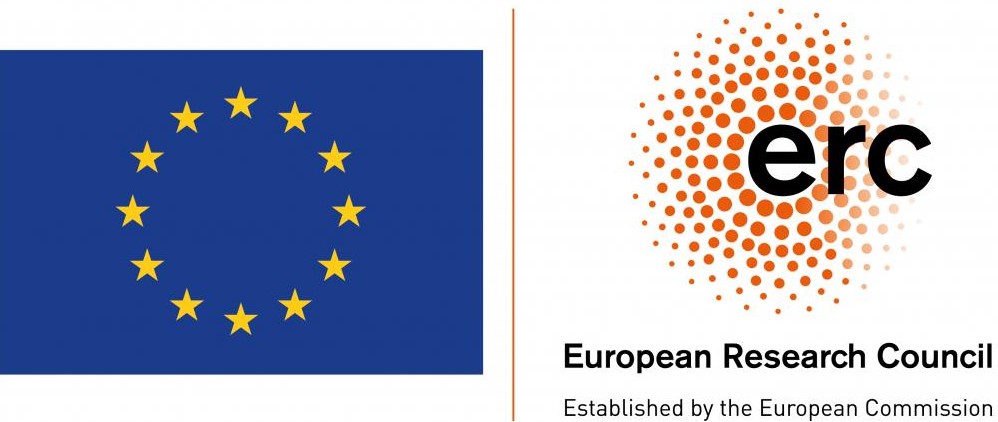